About usDiscover additional information about our company.
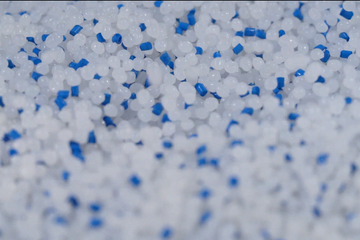
1.
SELECTION OF PELLETS & DEHUMIDIFYING
The production process begins with meticulous polymer selection, ensuring the highest quality materials are chosen. Our team possesses extensive expertise in plastic processing, forming the foundation of our manufacturing process. The polymer, supplied as colorless pellets, undergoes a crucial step of careful drying before extrusion. Given the high sensitivity of the granulate particles, a dedicated drying system is employed.
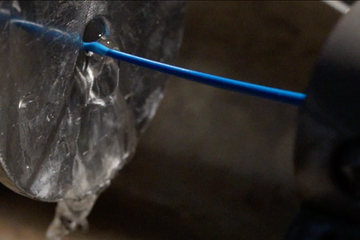
2.
EXTRUSION
The extruder plays a vital role in ensuring the polymer is effectively homogenized throughout the filament production process. As the pellet enters the extruder, it passes through multiple heated zones, facilitated by a plastification screw. This controlled heating process allows the material to melt and seamlessly combine with color pigments or other desired additives. Maintaining precise pressure control is crucial for achieving a homogeneous filament with a consistent diameter, ensuring the quality and integrity of the final product.
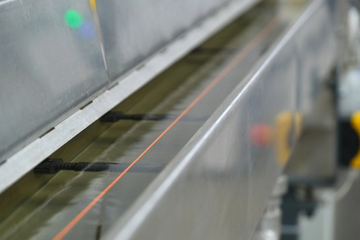
3.
COOLING
Cooling is an integral and essential stage of the production process, playing a crucial role in maintaining temperature control and preserving the pH of the coolant. The temperature and quality of the coolant have a significant impact on the final product. The initial cooling step, known as the "warm" bath, prevents uncontrolled shrinkage of the material while ensuring optimal surface quality. In the final step, the filament is carefully fed into a cold water bath, facilitating efficient heat dissipation from the strand, further enhancing the overall quality of the filament.

4.
DIAMETER MEASUREMENT
Unlike typical filament manufacturers, we employ a state-of-the-art two-axis laser micrometer for measuring our filaments. To be sure that the measurement result is reliable we use certified laser meter devices designed by worldwide known and reputable German company.
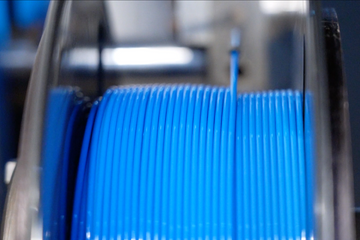
5.
WINDING PROCESS
We understand the frustration and time wasted when dealing with tangled or poorly wound filaments, which is why we have developed a proprietary system to ensure our spools are perfectly wound for neat and tangle free printing.
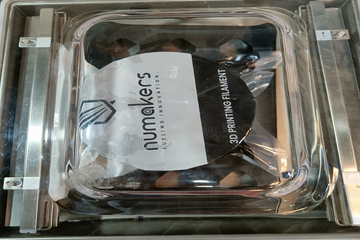
6.
PACKING
Each filament spool is vacuum packed inlcuding silica gel desiccant. For vacuum packaging we use foil with ZIP lock, what allows end-user to pack the filament precisely after using and prevent moisture absorption. Each spool contains information on the type of material, diameter and recommended printing temperature. At the end filament is placed in a cardboard box, which is additionally shrink wrapped.